It’s been a hard few months on MAGPIE. Constant component breakdown, electrical failures, maintenance periods and attempting to bring on-line some of the most complex diagnostics we’ve ever dreamed up have made progress slow and data scarce.
The charging barrel, full with transformer oil. Eight cables (not shown, they would attach to the brass cylinders at the top) take the two polarities (positive and negative voltages) to each of the four banks. The pneumatics are part of the safety system that only allows charging when all the doors are secured.
The latest failure was our charging barrel, a barrel of transformer oil full of bulky resistors, charging rails and pneumatics. When we started charging the Marx banks for a shot on Wednesday we heard an awful crackling wail coming from this barrel, and the voltage was leaking out of the Marxes like water through a sieve. In the darkness, we could see the tell-tale flicker of a coronal discharge, as streamers of ionised material sparked between conductors.
Not good. We scrubbed the oil, and left it to settle, but to no avail. Then this morning over tea, one of the senior researchers in the group suggesting ‘sparging’. I’d never heard of this, and giggled. But apparently it’s the process of bubbling an inert gas through a liquid to remove dissolved impurities, the idea being that our oil was contaminated with dissolved water. My advisor looked a little sceptical, but it seemed like an easy thing to test.
As a good scientist, I did a quick literature review, and turned up a paper from Sandia National Labs in 1999. Sandia are the big boys of pulsed power (high voltage, short time) engineering, so if they’ve tried this technique it must be legit. They even had the very relevant line:
“The component failures caused by poor oil performance were indistinguishable from normal Marx system failures that occur as components age. This may explain many random system faults previously attributed to component failure.”
I showed the paper to Sergey and rushed downstairs to build a sparging unit.
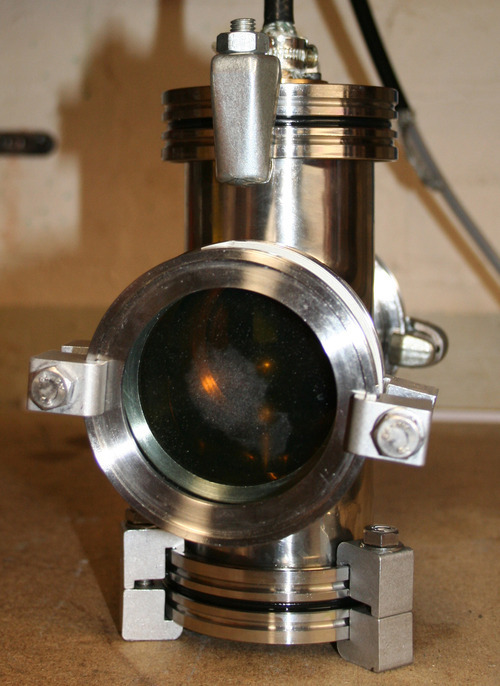
Our ‘oil torturer’, filled with oil and ready for testing. The little glass window lets us see the sparks when the oil breaks down as high voltage is placed between the submerged brass electrodes.
We already had a test unit for seeing how good a batch of oil is at holding off high voltages. It’s a little chamber with two brass balls inside, one grounded and the other charged by the dump barrel. With some of the contaminated oil from the charging barrel we could hold off 6.5 kV, which is pathetic.
Mk 1 Hare Industries Sparge-a-tron 9000, with ballast nut. It fits the bottom of the bucket perfectly.
I coiled up some plastic pipe into a spiral, cable tied it to a sheet of metal, added a big nut for ballast and got some vicious looking hypodermic needles we had lying around to puncture holes in it. By this point one of the postdocs had got in, and our enthusiasm was high. We filled a bucket with contaminated oil, turned on the nitrogen for half an hour and let it sparge away.
The oil bubbling merrily as nitrogen rushes through from the Sparge-a-tron underneath, dragging the dissolved water with it.
After this, we dumped the ‘clean’ oil back into the oil torturer and found it could hold off 30 kV, almost a five-fold improvement. Buoyed by success, we dropped the Hare Industries Sparge-a-tron 9000 ™ into the bottom of the charging barrel, and left it bubbling away. The volume is far larger, but after 90 minutes of thorough sparging, we found the oil could hold off 27 kV, a remarkable improvement. We tested the charging barrel, and weird noises and lights were gone. Success.
Bubbles at the top of a Marx bank from the improved Hare Ind./SwadTech Mk 2 Sparge-a-tron 9000 ™. My hand indicates the precarious position I’m balancing in.
Nitrogen is cheap as chips (£6 for a big bottle) so we built a large Sparge-a-tron that would fit inside a Marx bank out of a cable tray and some hefty nuts for ballast. We sunk that into the bottom of one bank and opened the bottle up. A huge rush of bubbles floated up through four metres of murky oil, driving a fast convection current and stirring the oil nicely. We’ll leave it overnight and test the oil in the morning to see how much nitrogen we’ll need to bring all the oil up to specification.